Everything you Need to Know About Ultrasonic Transducers
Are you familiar with the concept of ultrasonic transducers? These devices have an extensive range of applications in the industrial and medical fields due to being able to produce and receive ultrasonic vibrations.
These probes launch an electrical signal to a particular target, and when the signal hits the target, it travels back to the transducer. The ultrasonic wave frequency range is over 20 kHz. Such devices contain three essential components, including the piezoelectric crystal, the backing, and the wear plate.
Here is everything you need to know about Ultrasonic Transducers, their features, types, and uses.
What are they?
Ultrasonic transducers refer to devices that convert a certain type of energy into ultrasonic vibrations. They convert electrical signals to ultrasonic vibrations and waves focused on a particular object. When the transducer is supplied with electricity, it vibrates at a given frequency and produces sound waves with a frequency of 40 kHz.
The sound waves travel in a particular direction, and in the event of an obstacle on their path, an echo is produced. They bounce back to reach the transducer, which transforms the echo into an electrical signal. This device is capable of calculating the distance between it and the object by considering the time interval between the release of the original sound wave and the echo.
Moreover, such probes are considered more advantageous than infrared sensors due to not being affected by smoke or black particles in the surroundings. They have also proven to be better interference suppression from the background when compared to infrared sensors.
Types
Ultrasonic transducers are available in different types, sizes, features, and shapes. For instance, dual-element devices contain two crystal elements only separated with the help of an acoustic barrier. One of these elements is responsible for generating sound waves, while the other takes the role of a receiver. These elements are positioned towards each other to create a sound path in the shape of the letter V. Read more about the production and traveling of sound waves.
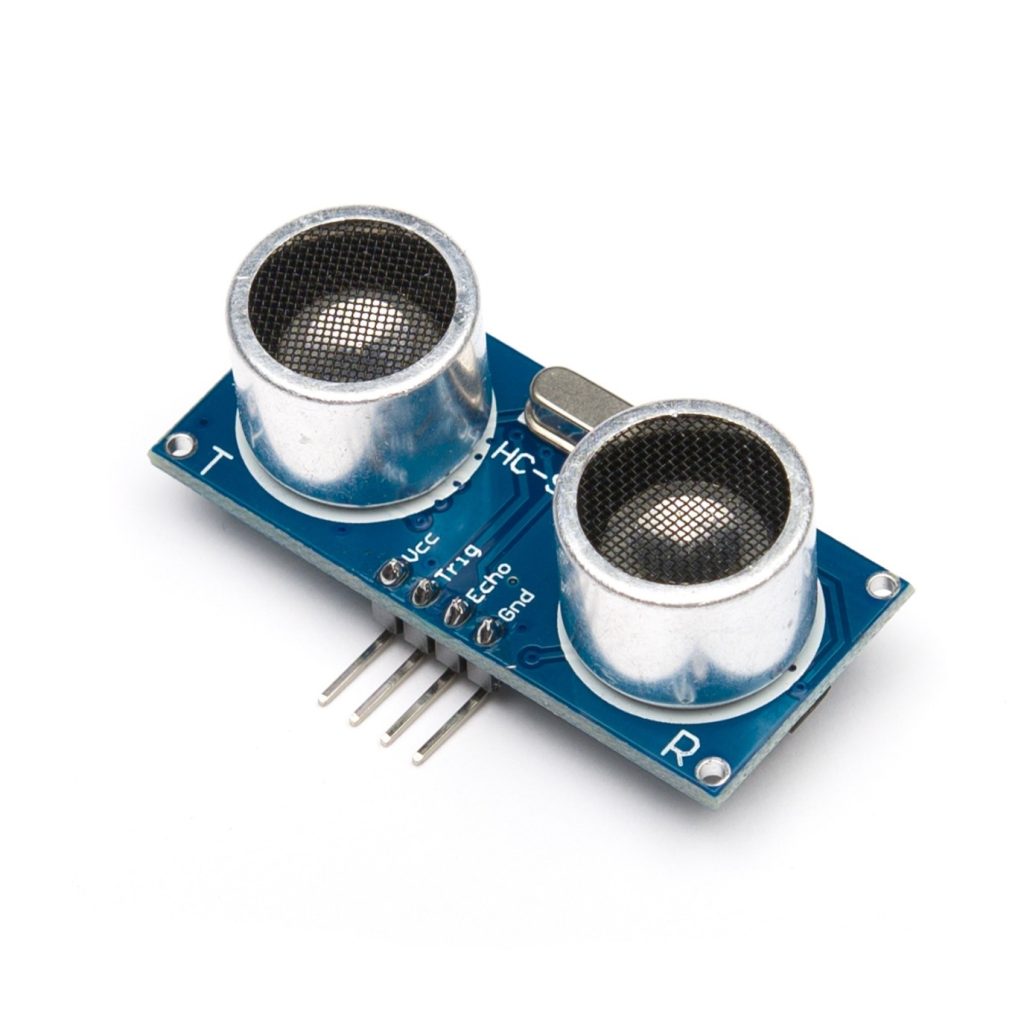
Furthermore, this results in the creation of a pseudo-focus effect, enhancing focal zone resolution. The increase in sensitivity is useful in examining parts whose back wall surface is rough. Consequently, dual-element models have corrosion applications by measuring wall thickness. Other applications of this probe include detection of cracks, porosity, laminations, and inclusions in forgings and castings, detection of cracks in bolts, weld overlay inspection, etc.
Contact ultrasonic transducers, as the name explains, are used for direct contact inspections. These devices consist of a single element with a wear-resistant surface that comes in contact with most metals, hence suitable for use in industrial environments. They are used for thickness gaging, delamination detection and sizing, velocity measurements, etc.
Another type of single-element ultrasonic transducer is the angle beam model. It’s used with a wedge to introduce a longitudinal or refracted shear wave into a piece for testing. This wedge introduces sound at a specific angle into the part. Such probes are commonly used by inspectors for weld integrity testing, flaw detection, sizing of cracks, etc.
Delay line ultrasonic transducers also consist of a single element. They ensure a time delay between sound wave generation and reflected waves arrival. Such high frequency is beneficial for the measurement and inspection of thin materials. The most common industrial applications include flaw detection, inspecting parts with limited contact areas, precision thickness gaging, and others.
Immersion models are designed to operate in water. The immersion technique offers rapid coupling, which allows inspectors to scan parts quickly. Their applications involve high-speed flaw detection, material analysis, in-line thickness gaging, etc. Conversely, linear models feature a linear piezoelectric crystal arrangement, whereas the beam shape is rectangular. These are versatile and have numerous applications.
Phased array ultrasonic transducers have gotten their name after the piezoelectric crystal arrangement named phased array. The central frequency of these models is between 2 MHz and 7.5 MHz, which classifies them as low frequency.
Features
The core of such probes is a piezoelectric chip in a metal or plastic jacket. The wafer is made from different materials. The wafer size is different as well, which influences the performance of each type of probe. There are several performance indicators, including working frequency, operating temperature, and sensitivity.
The working frequency refers to the wafer’s resonance frequency. Sensitivity depends on the way the wafer was manufactured. These devices can detect non-metal and metal objects, colored and transparent objects, liquid, powdery, and solid substances. Their abilities of detection aren’t affected by environmental conditions.
Applications
Ultrasonic transducers have a wide range of uses, particularly in the medical and industrial fields. As far as the medical field is concerned, these probes are used for performing diagnostic tests, internal organ tests, oncology examinations, etc. Due to the vibrations produced by these devices, they’re capable of removing kidney and bladder stones. Such probes also enable Doppler motion studies.
For example, liner models are used for venipuncture, vascular examination, laparoscopy, thyroid, and breast examinations. Convex models are used for the diagnosis of organs and abdominal examinations. Phased array probes are essential for cardiac and abdominal examinations.
In the industrial field, ultrasonic transducers assist production line management, liquid level assessment, flaw detection of different materials, an inspection of metallic and non-metallic components, thickness gaging, etc. Additionally, these devices are used for ultrasonic cleaning of surgical instruments, jewelry, dentures, and small machinery.
Chemical uses are common for these probes, as ultrasound assumes the role of a catalyst in multiple chemical reactions, including oxidation, polymerization, depolymerization, hydrolysis, and molecular rearrangement. Its role as a catalyst allows chemical processes to be performed at low temperatures and much faster than before. Some vital advantages of ultrasonic transducers are their ability to measure different materials, be resistant to temperature, dust, and water variations, measure high distances, and function in any type of environment.
The bottom line
The importance of these probes in the industrial and medical fields is indispensable.
They are used for various purposes for effective task completion!
Share It on :